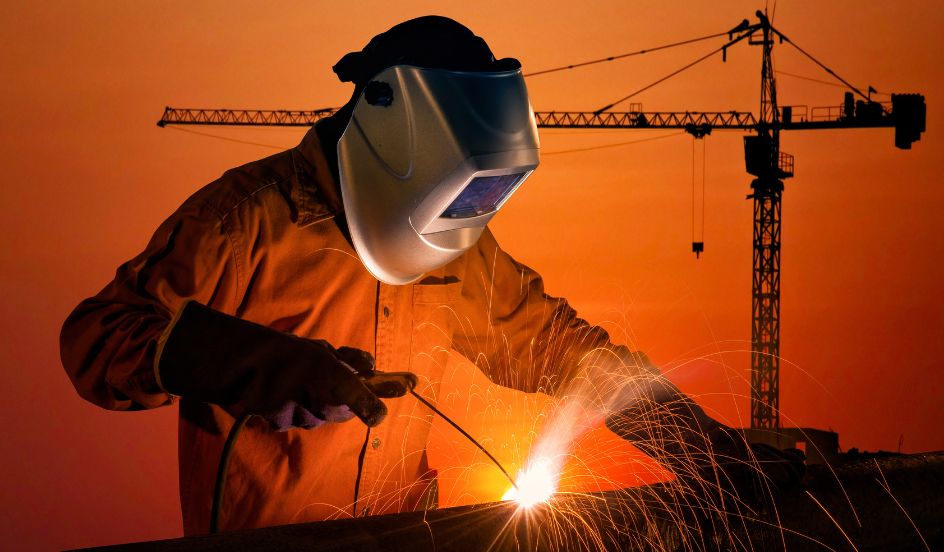
5 Common Welding Mistakes That Can Cost You Money and How to Avoid Them
Welding is a critical process in metal fabrication, and mistakes can lead to more than just an imperfect product. Errors during welding can cause costly rework, additional cleanup, and even production delays. To optimize your welding operations and reduce expenses, here are five common mistakes to avoid and expert advice on how to prevent them.
1. Improper Machine Setup
Incorrect machine setup or application parameters often result in poor weld performance. This can lead to issues like increased spatter or incomplete fusion, requiring costly rework. To prevent this:
- Establish procedures that specify the correct voltage and wire speed.
- Invest in welding machines with preset parameters to eliminate guesswork.
- Seek guidance from equipment distributors if you’re unsure about proper settings.
2. Faulty Cables or Connections
Loose or damaged cables can impact welding quality by causing voltage drops, resulting in inconsistent arcs and spatter. To avoid these issues:
- Inspect and tighten cable connections regularly.
- Replace damaged cables promptly.
- Check connections periodically to prevent wear and tear from escalating.
3. Improper Gas Flow or Pressure
Incorrect gas flow or shielding pressure is a frequent cause of weld defects. High gas pressure can result in spatter and incomplete fusion, while low pressure may leave the weld pool unprotected. Follow these best practices:
- Maintain proper gas pressure based on your application.
- Keep gas lines as short as possible to minimize surges.
- Position the regulator near the feeder to stabilize gas flow and pressure.
4. Neglecting Preventative Maintenance
Skipping regular maintenance is one of the easiest ways to let problems escalate. To keep your welding operations efficient:
- Inspect connections, cables, and consumables routinely.
- Replace worn-out parts such as contact tips, gas diffusers, and liners.
- Clean equipment regularly and track component lifespan for timely replacements.
5. Excessive Use of Anti-Spatter Spray
While anti-spatter spray can help prevent weld spatter from sticking, overuse or misuse can harm weld quality. Excess spray can enter the weld joint, leading to poor penetration and added rework. Best practices include:
- Use the correct amount of anti-spatter spray for your application.
- Avoid soaking welding gun consumables in anti-spatter to prevent premature wear.
Why Choose Beniko Industries?
Beniko Industries has extensive experience delivering high-quality welding and metal fabrication services. From proper machine setup to precision welding, our skilled team ensures the best results while optimizing costs.
Get started today! Request a Quote to learn how our welding solutions can benefit your next project.