Blog
- Home
- Steel Fabrication
- 9 Common Welding Problems and How to Fix Them
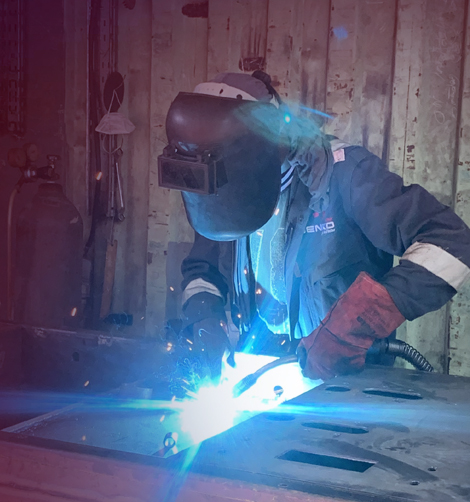
9 Common Welding Problems and How to Fix Them
Welding plays a critical role in metal fabrication, but it comes with its challenges. Without the correct technique, several common problems can arise. Here are the top nine welding issues and the best solutions to fix them:
1. Spatter
Spatter occurs when molten material droplets form near the welding arc, common in gas metal arc welding (GMAW). To prevent this, reduce the welding current, adjust the arc length, and ensure correct gas shielding. Proper polarity settings and regular cleaning of the gas nozzle also help.
2. Porosity
Porosity is caused by trapped gases in the weld, leading to weak spots. It can be avoided by using dry, clean materials and ensuring the correct welding torch angle. Re-baking consumables and ensuring proper gas shielding also reduce porosity.
3. Undercut
Undercutting results from high arc voltage or long arcs. Avoid this by slowing down the weld speed, monitoring weave patterns, and using the correct electrode size. Proper technique reduces the risk of excess molten metal causing an undercut.
4. Deformation
Deformation occurs as welded metals cool and contract. Prevent this by welding from both sides of the joint, using large electrodes, and clamping firmly. Adjusting the weld sequence and making fewer passes also reduces deformation risk.
5. Cracks
Cracks in welds can grow over time, weakening the joint. Prevent cracks by thoroughly cleaning and prepping materials, reheating both sides of the joint, and testing machine settings for proper heat levels before welding.
6. Incomplete Penetration and Fusion
These issues arise when welds fail to fully fuse on one or both sides of the joint. To solve this, use a wider root gap and ensure the electrode size matches the root width. Lowering travel speed and weaving between plate edges can also help.
7. Slag Inclusions
Slag inclusions occur when flux particles become trapped inside the weld. Use well-maintained consumables, correct welding parameters, and proper arc settings to avoid this problem.
8. Incorrect Wire Delivery
Improper wire delivery can cause chattering sounds during welding. Prevent this by ensuring the correct tip size, replacing worn tips, and properly aligning drive rolls and guide tubes.
9. Brittle Welds
Brittle welds result from using incorrect or bare electrodes. To produce ductile welds, use shielded arc electrodes, avoid excessive current, and ensure multiple weld passes are made.
Beniko Industries | Expert Welding Services
Need professional welding services with minimal distortion? Beniko Industries specializes in MIG & TIG welding of steel, stainless steel, and aluminum. Our use of pulsed welding machines ensures controlled heat, minimal distortion, and superior quality. We also offer in-house services like weld inspection, stainless steel polishing, and testing of watertight enclosures. Certified to AWS D1.1 & D1.6 standards, our team guarantees precision and durability.