Blog
- Home
- Powder Coating
- Powder Coating Process Explained: Pretreatment to Curing
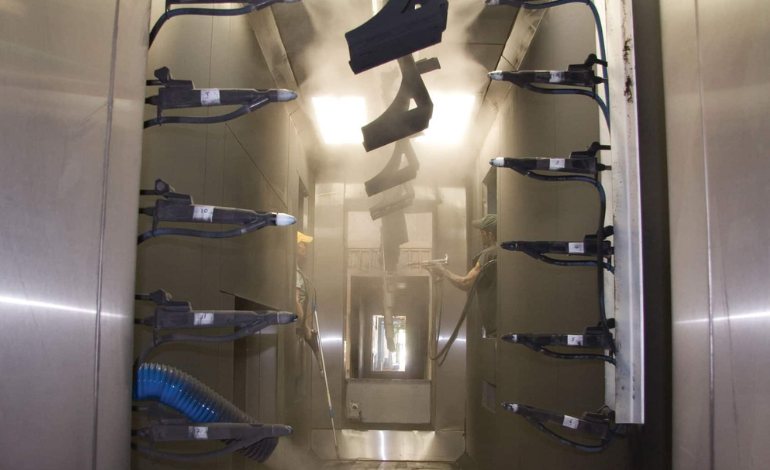
Powder Coating Process Explained: Pretreatment to Curing
Powder coating is a popular finishing technique known for its durability, vibrant finishes, and eco-friendly attributes. If you’ve ever wondered how this fascinating process works, from the initial preparation to the final curing stage, this blog post is your comprehensive guide to understanding the powder coating process, step by step.
1. Surface Preparation - The Foundation of Success:
The journey of a powder-coated finish begins with meticulous surface preparation. This step is crucial to ensure adhesion and longevity. Here’s what happens:
- Cleaning: The substrate, typically metal, undergoes thorough cleaning to remove dirt, oil, rust, and other contaminants. This is often done using alkaline cleaners or a phosphate-based solution.
- Rinsing: After cleaning, the surface is rinsed to remove any residue from the cleaning process.
- Drying: The cleaned surface is dried completely to prevent any moisture-related issues during the powder coating process.
2. Pretreatment - Promoting Adhesion and Corrosion Resistance:
Pretreatment serves multiple purposes, including enhancing adhesion, providing corrosion protection, and promoting powder coating uniformity. Common pretreatment methods include:
- Phosphating: A phosphate conversion coating is applied to the metal surface. It not only enhances adhesion but also provides corrosion resistance.
- Chromate Conversion: This method, often used for aluminum, creates a thin film on the metal surface that improves adhesion and protects against corrosion.
3. Application of Powder:
Once the surface is properly prepared and pretreated, the next step involves applying the powder coating. Here’s how it’s done:
- Electrostatic Application: A spray gun charges the powder particles with a positive electrostatic charge. The grounded substrate attracts these charged particles, ensuring an even and uniform coating.
- Manual or Automatic Application: Depending on the scale of the project, powder can be applied manually or with automated equipment, such as robots for precision coating.
4. Powder Coating - The Beauty of Electrostatic Attraction:
As the charged powder particles are drawn to the grounded surface, they adhere to it, forming a uniform coating. The electrostatic attraction ensures that the powder covers all exposed areas, including recesses and corners, resulting in a smooth and even finish.
5. Curing - Turning Powder into a Durable Coating:
The final step in the powder coating process is curing, which transforms the powder into a hardened, durable finish:
- Heat Application: The coated parts are placed in an oven or curing chamber, where they are subjected to high temperatures (typically between 350°F to 450°F or 175°C to 232°C). This heat causes the powder to melt and flow, forming a continuous film.
- Cross-Linking: As the powder melts, chemical reactions occur within the coating, creating strong cross-links between the polymer molecules. This process enhances the coating’s durability, hardness, and resistance to chemicals and UV radiation.
- Cooling: After the curing process, the coated items are allowed to cool slowly, ensuring that the finish solidifies properly.
6. Inspection and Quality Assurance:
The final step involves a thorough inspection of the powder-coated items. Quality control checks are performed to ensure that the coating meets the desired thickness, appearance, and adherence standards.
Conclusion - A Finish That Lasts:
The powder coating process, from surface preparation to curing, is a meticulously orchestrated sequence of steps that results in a durable, vibrant, and long-lasting finish. Whether applied to automotive parts, outdoor furniture, architectural elements, or industrial equipment, powder coating’s impressive qualities make it a preferred choice for enhancing the aesthetics and durability of various products. So, the next time you admire a flawlessly coated object, you’ll have a deeper understanding of the intricate process that makes it possible.