Blog
- Home
- Steel Fabrication
- Understanding the Welding Techniques in Steel Fabrication
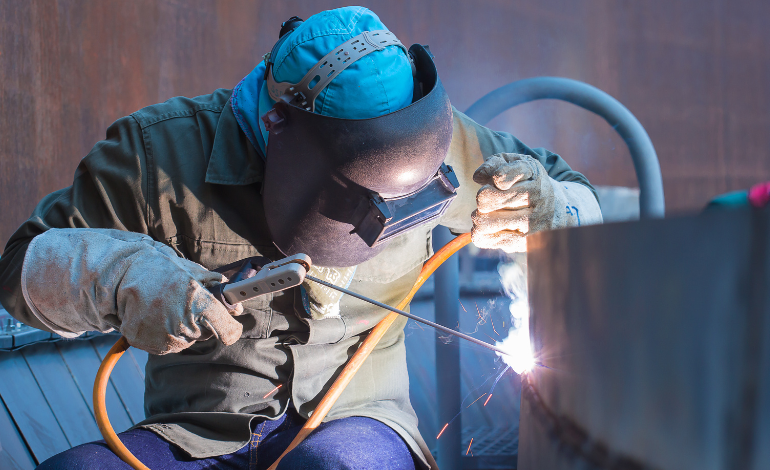
Understanding the Welding Techniques in Steel Fabrication
Steel fabrication, a process that involves the cutting, bending, and assembling of steel structures and components, is a fundamental aspect of various industries, including construction, manufacturing, and infrastructure development. Welding, a critical part of steel fabrication, joins separate steel pieces to form a cohesive and robust structure. In this blog post, we delve into the world of welding techniques used in steel fabrication, understanding their principles, applications, and advantages.
The Basics of Welding:
Welding is a fusion process that joins metals by melting their edges and fusing them together. In steel fabrication, welding creates a strong bond between steel components, providing stability and strength to the overall structure. Different welding techniques exist, each offering unique benefits depending on the project’s requirements and the types of steel involved.
Shielded Metal Arc Welding (SMAW):
Shielded Metal Arc Welding, commonly known as stick welding, is one of the oldest and most widely used welding techniques in steel fabrication. In SMAW, an electric arc is created between the steel electrode (stick) and the base metal, causing the electrode to melt and form a weld bead. This method is versatile and suitable for various steel thicknesses, making it popular in construction, maintenance, and repair work.
Gas Metal Arc Welding (GMAW):
Gas Metal Arc Welding, also known as MIG (Metal Inert Gas) welding, employs a continuous wire electrode fed through a welding gun. Simultaneously, an inert gas shield, usually argon or a mixture of gases, protects the weld from contamination. GMAW offers high productivity and is commonly used in automotive, manufacturing, and fabrication industries.
Gas Tungsten Arc Welding (GTAW):
Gas Tungsten Arc Welding, or TIG (Tungsten Inert Gas) welding, utilizes a non-consumable tungsten electrode to create the arc. As in GMAW, an inert gas shield protects the weld. GTAW produces precise and clean welds, making it ideal for intricate steel components and critical applications in aerospace, electronics, and artistry.
Flux-Cored Arc Welding (FCAW):
Flux-Cored Arc Welding is similar to GMAW, but instead of using a solid wire, it employs a tubular wire filled with flux. The flux creates a shielding gas, protecting the weld from contamination and allowing for better performance in windy or outdoor conditions. FCAW is often used in heavy industrial applications and construction.
Submerged Arc Welding (SAW):
Submerged Arc Welding involves feeding a continuous wire electrode into the weld joint while covering it with a layer of flux. The welding process occurs beneath the flux layer, providing excellent protection from atmospheric contamination. SAW is favored for thick steel plates and structural components due to its high deposition rates and deep penetration capabilities.
Laser Welding:
Laser Welding is a modern and precise welding technique that uses a focused laser beam to melt and join steel components. It is particularly suitable for thin and intricate steel parts where minimal heat input is crucial. Laser welding is employed in industries such as automotive, electronics, and medical devices.
Conclusion:
Welding techniques are the backbone of steel fabrication, enabling the creation of complex and robust structures that drive various industries forward. Each welding method offers unique advantages, making them suitable for specific applications and steel types. As technology continues to advance, so will the welding techniques, improving efficiency, quality, and safety in the steel fabrication process. Understanding the nuances of each welding technique empowers engineers, fabricators, and manufacturers to make informed decisions, ensuring the successful realization of innovative and reliable steel structures that shape the world around us.